During the COVID-19 crisis, Brad Rogers, a Process Engineer for Design Group in Modesto, California (US), has continuously supported a global supplier of soft drinks to ensure that water treatment and can production started earlier than planned to meet the market demand for water.
He successfully navigated a difficult and continuously changing environment to ensure production systems were fully supported to come up from a complete plant shutdown to meet quality standards for the product.
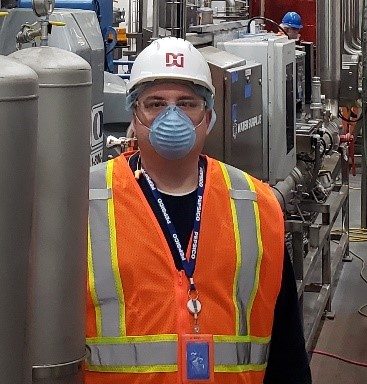
Meanwhile, Zach Vernon, Project Manager for Design Group’s Indianapolis office, oversaw the installation of two large tanks at the Indianapolis plant of a global soft drink supplier. The tanks were installed via crane after the plant’s roof was removed. Thanks to his diligent preparation and seamless coordination with multiple vendors, contractors and the client, the work was completed in a single day without impacting production.