We greatly appreciate you! Your hard work is really “putting the team on your back.”
Author: David McElroy
BW Heroes
Thank you to all those individuals who risk their own safety going into work each day! This helps ensure that the company and all internal and external customers have a bright future to look forward to. I cannot express my appreciation enough!
During the peak of the Covid19 situation my wife needed a kidney procedure performed and we were having difficulty finding an office willing to perform the task. Thankfully Dr. Stewart from Mount Carmel agreed to perform the procedure in spite of the current virus situation. The team was professional and responsive. Not only was the procedure performed soon and quickly, the follow up by Dr. Stewart was a breath of fresh air. He followed up with a phone call twice. My wife is doing well today thanks to his office and the hospital. Thank you.
Phil – Ohio
Thanks To Every BW Team Member
Thanks to everyone working at BW!! Those at home, those in the offices, those working hard to stay on top of how to handle this issue with COVID-19 – keeping our team members safe while working and creating a plan to bring everyone back to work safely. A VERY SPECIAL THANK YOU to the team members working at the facilities, keeping production moving….ensuring products are made and delivered to families in need. It is your hard work that is keeping this large family in place. At a time of economic downturn, BW is working to stay healthy and so many of you are on the lines ensuring that happens. God Bless Everyone and your families!!
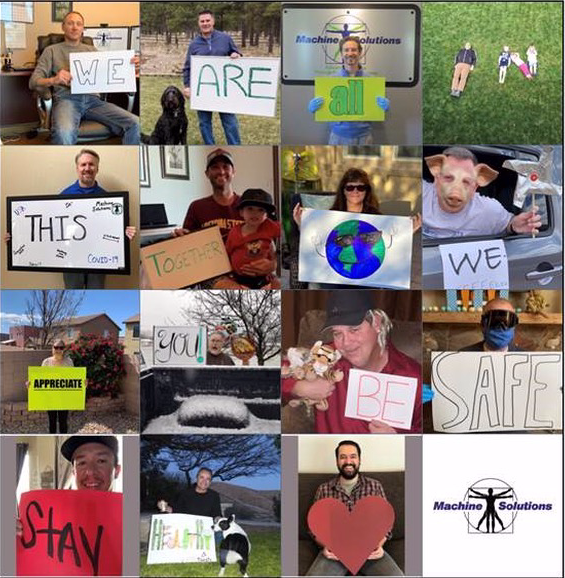
Headquartered in Flagstaff, Arizona (USA), Machine Solutions is a global supplier of process and testing solutions to the medical device industry. They have approximately 175 team members among their four locations/brand sites: MSI in Flagstaff; Steeger in Inman, South Carolina; Vante in Tucson, Arizona; and Plastic Weld Systems in Newfane, New York. To support their team members who remain onsite on split and varied shifts, some of those working from home collaborated to create the unique photo above. Neil Jaquez, Director of CPD, said they wanted to do something “to show the 130 team members who are keeping everything moving in our facilities that we are truly ALL in this TOGETHER.”
(Leave your own message of thanks to our team members who are working in our facilities or at client sites by clicking HERE.)
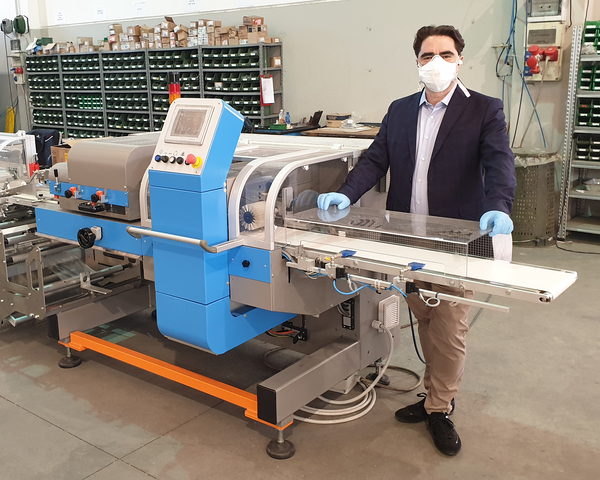
Schib, which manufactures automatic packaging lines and flow wrapper packaging solutions as part of BW Flexible Systems, is in Monte de Malo, Italy, about 60 miles (100 km) northwest of Venice. When Schib’s leadership team learned a local business would be producing much-needed facemasks for the global market, they wanted to help.
Alessandro Stiffan, Schib General Manager, said the contractor planned to convert his production of textile finishing products to the production of facemasks. To avoid purchasing a machine for the temporary facemask production, he reached out to Schib.
“We already had the availability of a Schib CO-50 machine—a good fit for that product—and we immediately lent it to this contractor for free,” said Stiffan.
“This was a clear application, in my mind, of our Guiding Principles of Leadership and our Safety Covenant: we want to foster care and safe practices within our families and communities, we measure our success by the way we touch the lives of people. It was our call and we responded. It is a tiny contribution, but every drop counts when there is an emergency.”
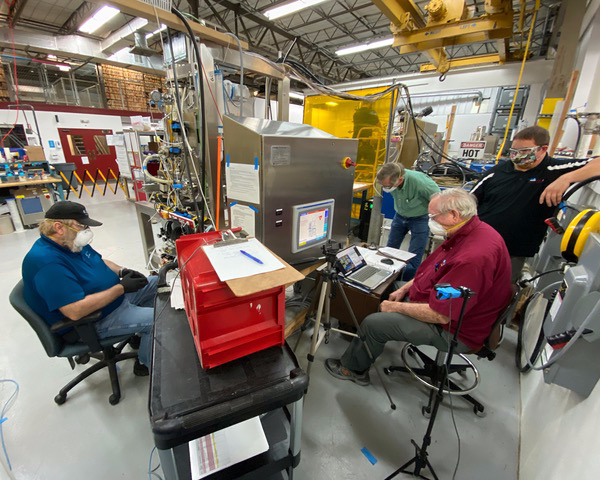
When travel restrictions made an onsite factory acceptance test (FAT) impossible, the CARR Centritech centrifuge team of Pneumatic Scale Angelus in Clearwater, Florida (USA) quickly transitioned to a virtual FAT for a Powerfuge for Merck. What originally was expected to take a week at the customer site was completed in just three days, resulting in a successful FAT and a thrilled customer!
Mike Welch, PSA’s Director of Centrifuge Sales, explained, “For pharmaceutical companies like Merck, any disruption to the supply chain can result in devastating regulatory delays or potential shutdowns that bring the development and delivery of vital medications and potential vaccines to a halt. For our team, it serves a great reminder that we all play a part in this fight and our work has far-reaching and meaningful effects.”
Steve Curran, Merck’s Associate Director of Engineering, said, “Your planning and execution of this virtual FAT is a great example of commitment to innovation and commitment to meeting the project goals for the benefit of the future patients this equipment will serve.”
Pictured, from L to R: Darris Stowers, Gerald Cummiskey, Paul Gregowicz (black shirt), and Jim Davis (green shirt)
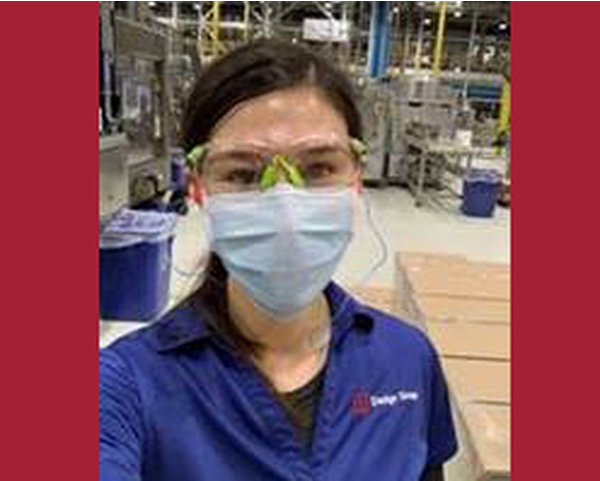
Melissa Heskett, a Design Group Project Engineer from the St. Louis office, has been providing both onsite and remote support to a key Personal Care Product client in Jonesboro, Arkansas (USA). From managing innovation projects to assisting in transitioning a haircare production line to producing hand sanitizer in the midst of COVID-19, Melissa has stepped up to support the customer’s shifting needs.
When fewer team members were left at the site due to COVID-19 remote work or needed time off as a result of a recent tornado, Melissa stepped in to support additional innovation trials onsite. She implemented new best practices to capture data for the Production and Quality Team and continues to work on tools, such as Workbooks, allowing the team to establish trial procedures, capture information and maintain organization. Melissa’s expertise and efforts have led to a six-month extension of services!
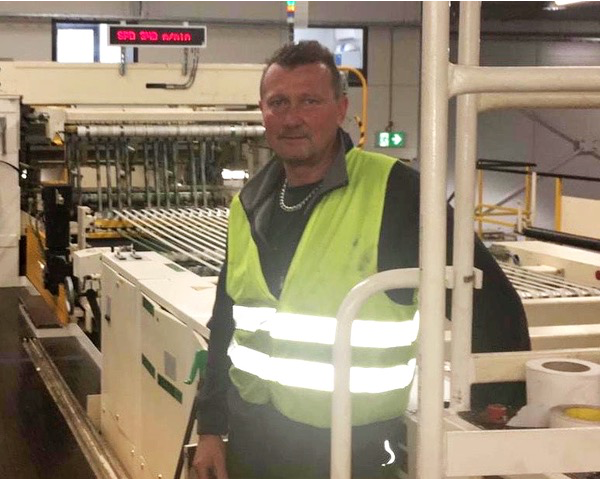
A customer in the Netherlands called the BW Papersystems Hamburg, Germany Helpdesk hotline on Good Friday, reporting noise and vibrations at the cross cutter section of their Jagenberg folio sheeter and newly installed knives being worn out after only one week. Shortly after, the sheeter stopped completely, resulting in production losses. Service at the site was necessary, despite COVID-19 restrictions. Fortunately, there had not been any COVID-19 outbreaks at the customer plant, thus far, and they had adopted high safety and hygiene measures for prevention.
On Easter Monday, BWP Service Engineer Jürgen Lorkowski, from their Neuss office (across the Rhine River from Düsseldorf), drove almost two hundred kilometers (~120 miles) to the site to fix severe damage due to a burnt bearing. The customer was relieved and thankful for the fast and onsite support during these challenging days. As a precaution, Jürgen is temporarily working from home, following internal safety protocols and continuing to follow WHO guidelines for monitoring his health.
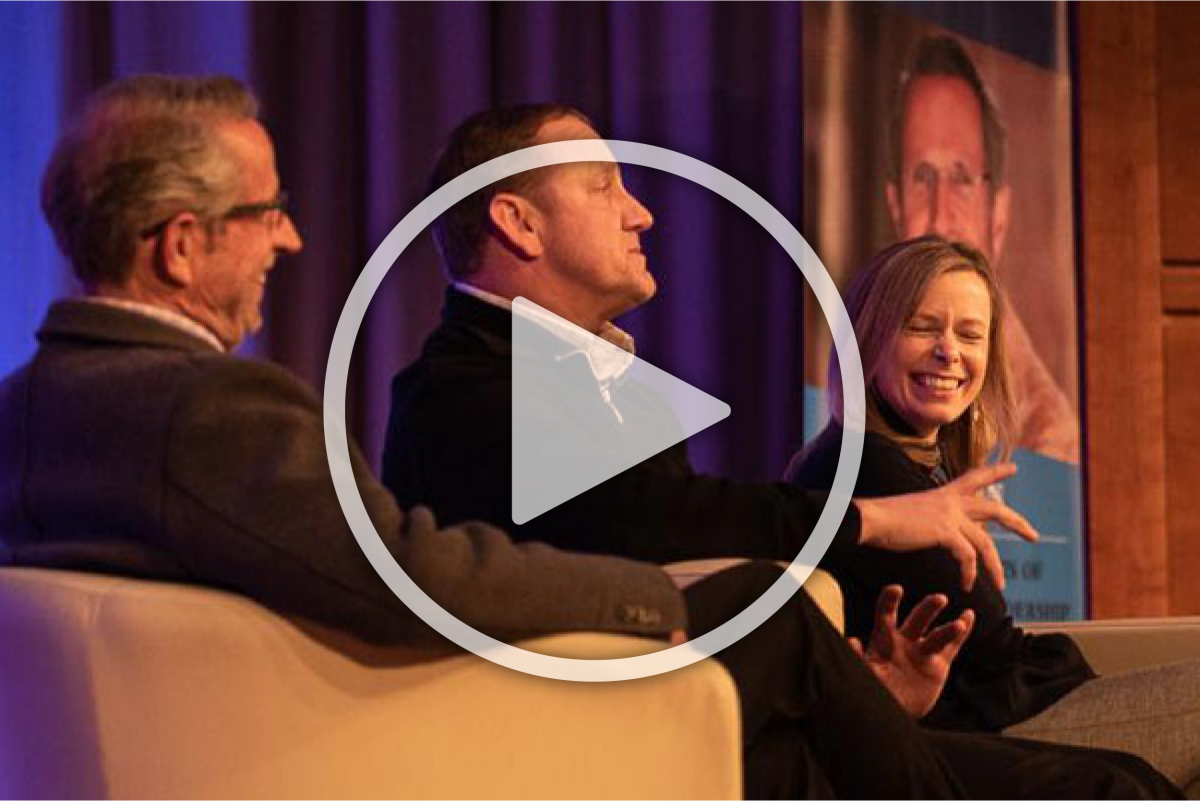
Enjoy a lively conversation between CEO Bob Chapman and Sara Hannah and Matt Whiat of Chapman & Co. discussing Barry-Wehmiller’s experiences in 2008-2009, how we applied those lessons to shape our response to the current crisis, and how we are navigating the COVID-19 pandemic.